Procurement & Supply Chain Excellence
A seamless flow of medical resources, from precise sourcing to efficient delivery.
Tailored
to your particularities and needs
High-end
to maximize impact
Strategic & tactic
to align operations and vision
Supply Chain key elements
The supply chain plays a pivotal role in ensuring the seamless flow of goods and services. It encompasses the entire process, from raw material procurement to end-user delivery. Efficient supply chains enhance competitiveness, reduce costs, and foster innovation, contributing significantly to economic growth and stability.
Healthcare organisations must optimize their Supply Chain
The impact of COVID-19 on the global medical supply chain is widely acknowledged. Today, hospitals grapple with shortages and quality concerns, despite significant efforts in supply chain management.
Enhancing collaboration, capitalizing on scale, and fostering synergies will fortify the resilience of the healthcare & life sciences sectors, ensuring a more robust response to future challenges.
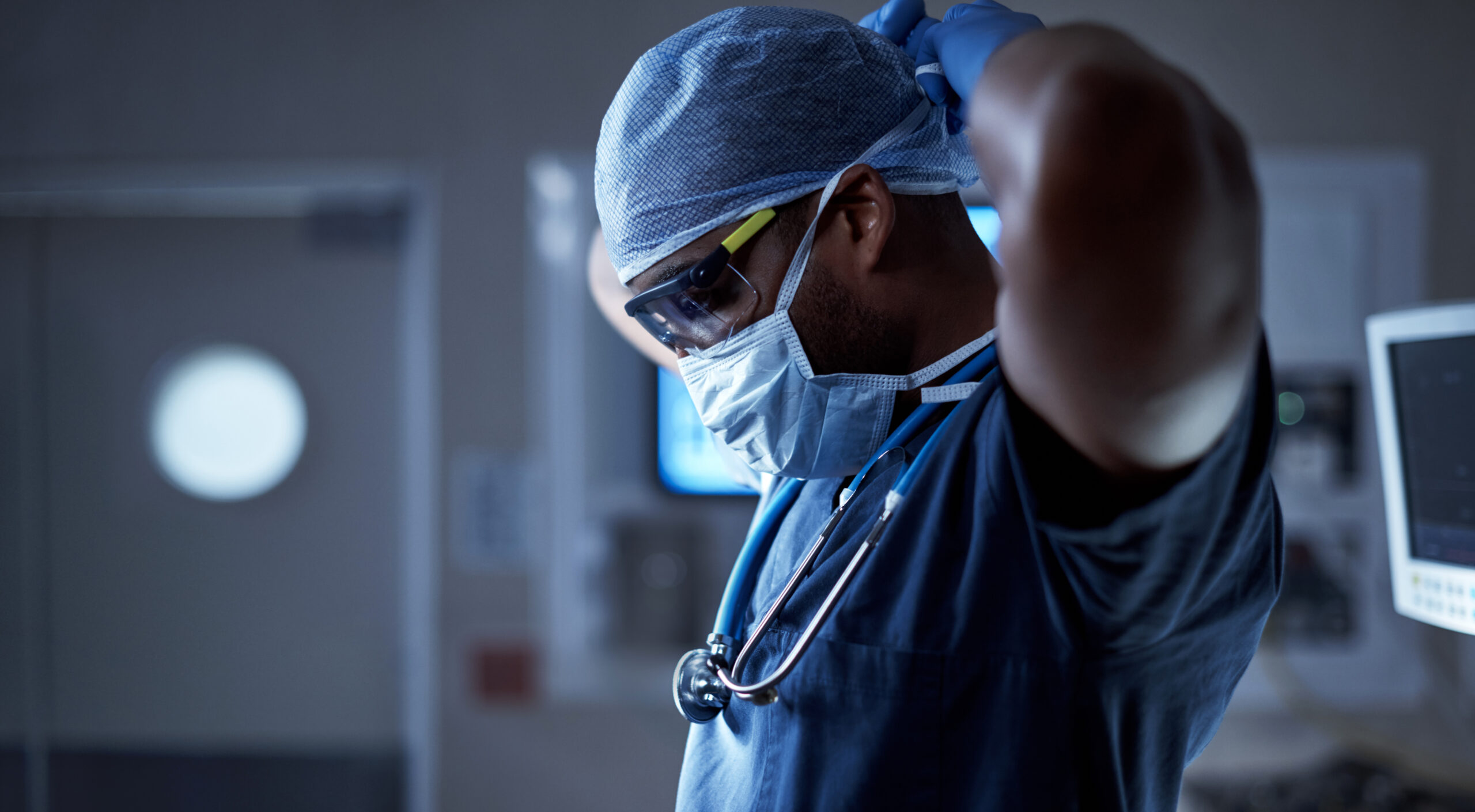
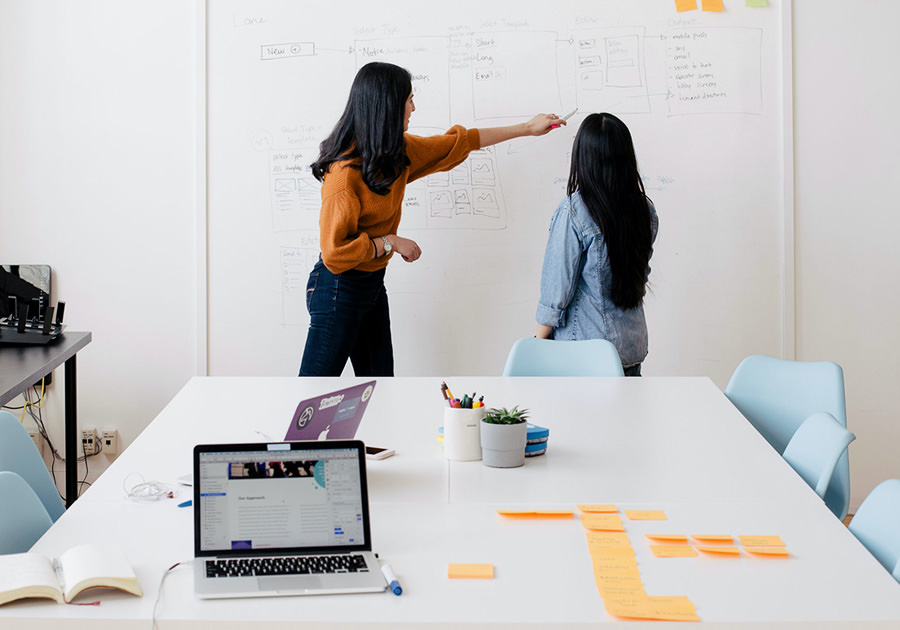
1st Phase
Analysis, concept & Business case
The initial phase serves as a crucial stage dedicated to analyzing, measuring, and capturing key elements aligned with your strategy and ambitions. This groundwork lays the foundation for formulating recommendations and crafting a detailed action plan to guide the transformation journey.
How do we operate ? We involve your collaborators and your management by conducting interviews, deep dive analysis, hosting workshops, and engaging in on-the-floor observations.
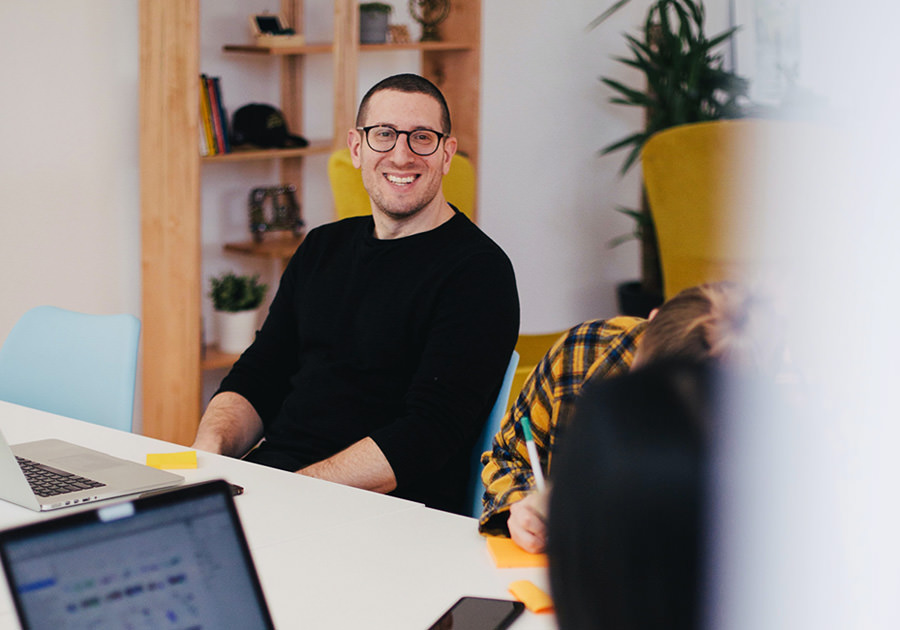
2nd Stage
Implementation
The second phase revolves around putting recommendations into action, working collaboratively with your teams on a day-to-day basis to ensure effective implementation and adoption (change management approaches). On the top of everything, we developp a performance management system to monitor the benefits of the implementation.
How do we operate ? We work together with your collaborators to defining, developing and implementing tailored solutions.
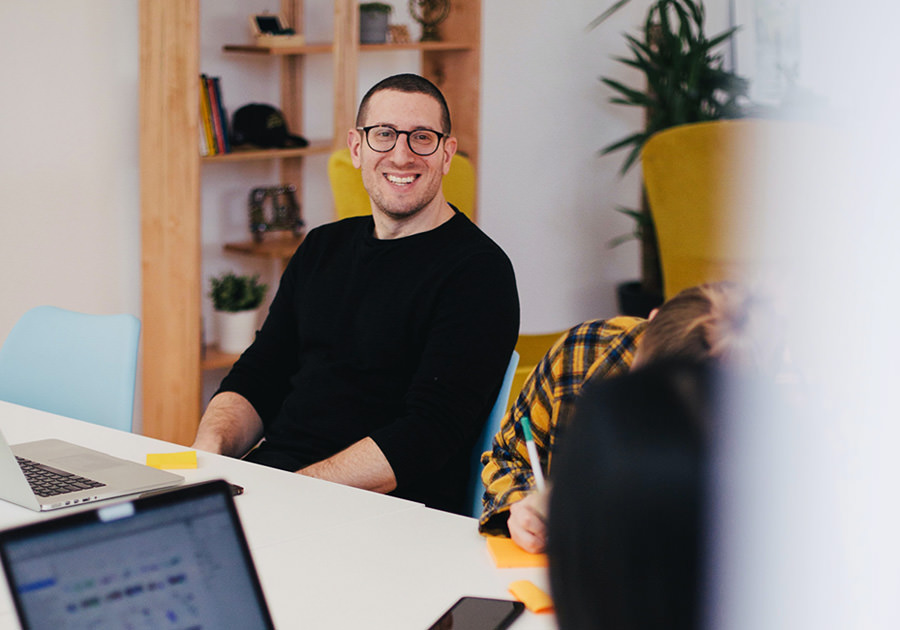
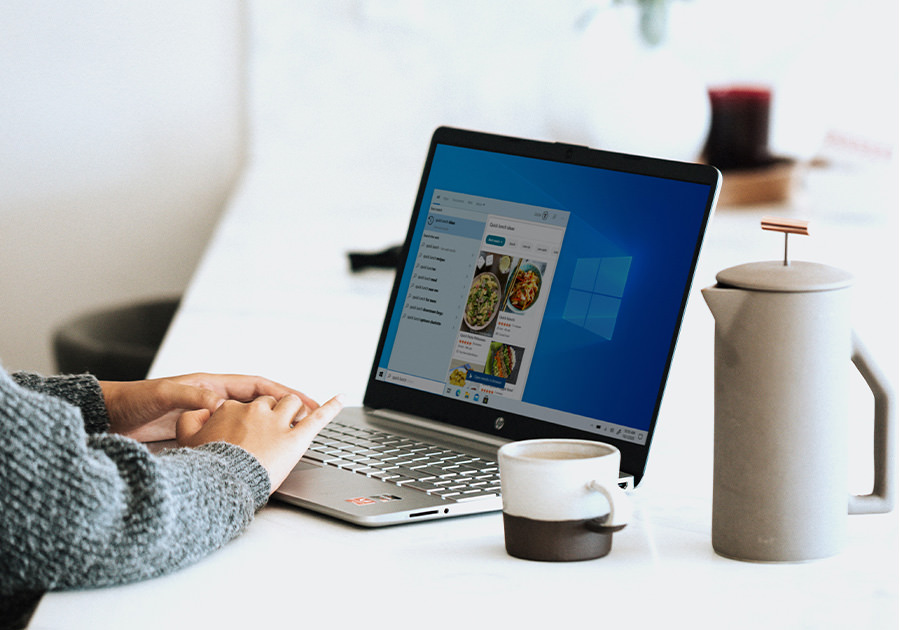
3rd Stage
Follow Up & Coaching
In the concluding phase, we emphasize the ongoing monitoring of implemented solutions to ensure sustained performance and effectiveness, ensuring your objectives are consistently met.
How do we operate ? We set up monthly touch point with you and your key collaborators to review and challenge the ongoing performance.
Supply Chain Transformation
A listed Aerospace Tier 1 supplying all major airline companies with state-of-the-art articles. Their Business Unit “Spare Parts” had to deal with a sharp increase of the demand, in addition to the volatility of this demand and the very high number of SKU, delays increased and OTD drop down. Some parts are sourced from suppliers while others are produced internally. The following sub-projects aimed to reduce delays by implementing simple management routines and business processes optimisation.
- Restructured and improved a spare parts business unit (considering departments Supply, Customer Service, AOG, Scheduling and Production) ;
- Reworked the layout and material flow to enhance productivity within the production workshop;
- Transformed the flow and processes for the logistic area (reception; control; packaging and expedition) to stimulate unique flow and thus efficiency of the warehouse;
- Analyzed the procurement Lead times, OTD, Demand pattern, ABC analysis and safety stock policy and root-cause analysis;
- Created a decision and simulation tool to help the procurement department to establish their improvement roadmap to prioritize suppliers actions with a lever on the OTD and Lead times;
- Created and implemented a Master Production Schedule (MPS) considering 3 processes and 12 workstations: Capacity (62FTE) and production scheduling tool creation, documentation, process implementation and coaching.
(Personal reference)
In Poland, fluctuations in demand led to adjustments in resource planning, resulting in the loss of experienced operators. As demand surged, the finishing (slitting) department became the bottleneck, causing significant delays in customer deliveries.
Efforts to outsource certain activities failed to meet quality standards. Aptare was brought in to assess the situation and implement initiatives to boost productivity.
- Standardized Machine Operations: Define and implement consistent machine speed parameters for each product type.
- Enhanced Operator Training: Harmonize operator workflows through clear, standardized processes and training.
- Shift Supervision: Introduce supervisory roles to ensure adherence to standards and facilitate continuous improvement.
- Resource Allocation: Optimize FTE allocation to cover shift requirements fully.
- Continuous Improvement Culture: Build a mindset of proactive problem-solving through structured CI programs.
Automatisation & robotic program
A major parcel delivery company operated their European Hub located in Belgium with 15-year old system. In order to keep up with the competition, guarantee a service level to the customer at a lower operating cost, they decided to refurbish the existing hub with state-of-the-art equipment.
This is a >€85M programme impacting the Business-As-Usual (BAU) activities.
We supported this program in :
- Created and Managed an Integrated planning, and ensured cohesion and coherence; Risks management (over 250 risks mitigated), Change Management and reporting.
- Set up a role for planning the arrival of people (Suppliers and Sub-contractors) and material considering the multiple constraints of a restricted access area (airport area); Created an Access tool to support this role and enable reporting.
- Implemented a documentation process to support the whole program
(Personal reference)